The customer is a customs agent looking after shippers handling vehicle parts. Due to ship delays during the COVID-19 pandemic, the shortage of ship space and the container shortages, exports did not progress as scheduled (the shipper could not get export bookings soon, only well into the future).
Production continued due to high demand at export destinations, but exports were not possible and products accumulated in the shipper’s warehouse, which began to affect their production system.
Exports were not proceeding as scheduled and cargo accumulated in the shipper’s warehouse. We proposed temporary storage to solve this.
Industry | Customs clearance business |
---|---|
Type of cargo | Auto parts |
Purpose | Container storage (warehouse space improvements), drayage |
Transportation area | North America and Europe |
Due to the impact of ship delays during the COVID-19 pandemic, the shortage of ship space and the container shortage, cargo was stuck in the shipper’s warehouse. Although production continued because needs at export destinations were uninterrupted, cargo just accumulated because exports were not possible. We were asked if we could solve this situation.
- Impacted by the COVID-19 pandemic, exports did not progress as scheduled.
- Products accumulated in the shipper’s warehouse because they could not be exported.
- The customer stores containers at Nishihama Van Pool until the terminal opens.
- We also proposed short drayage between Nishihama Van Pool and the terminal.
- We were able to alleviate the tight situation in the shipper’s warehouse.
- We were able to spread the load by doing work in advance and meet deadlines.
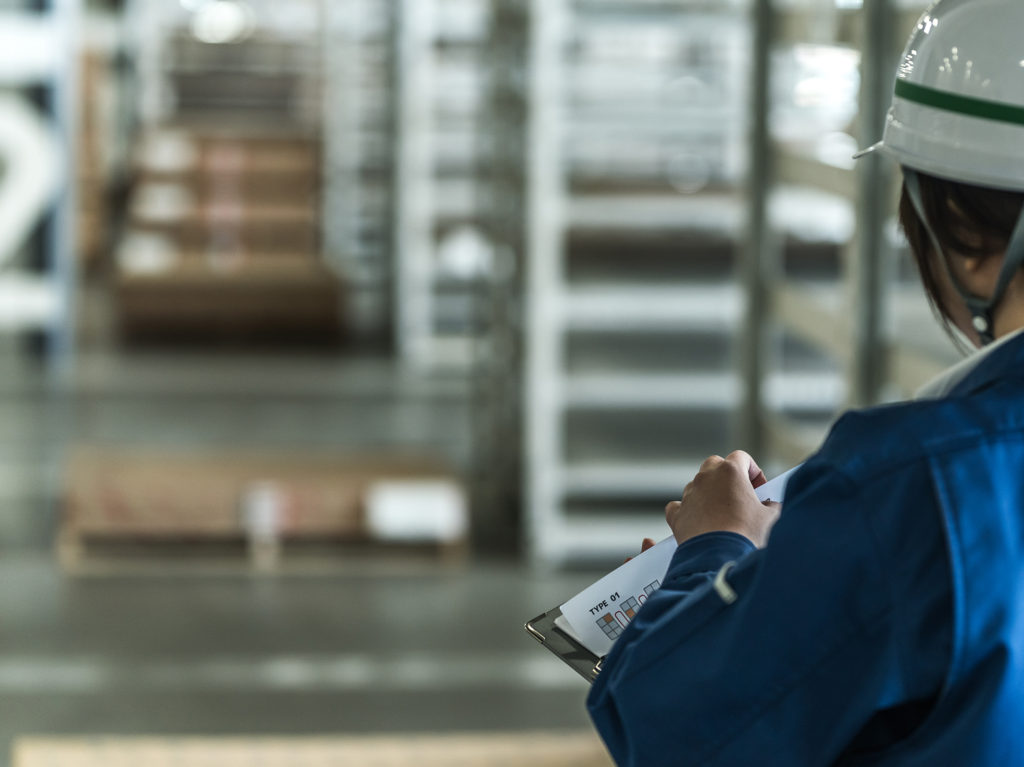
Exports were not proceeding as scheduled and products accumulated in the shipper’s warehouse.
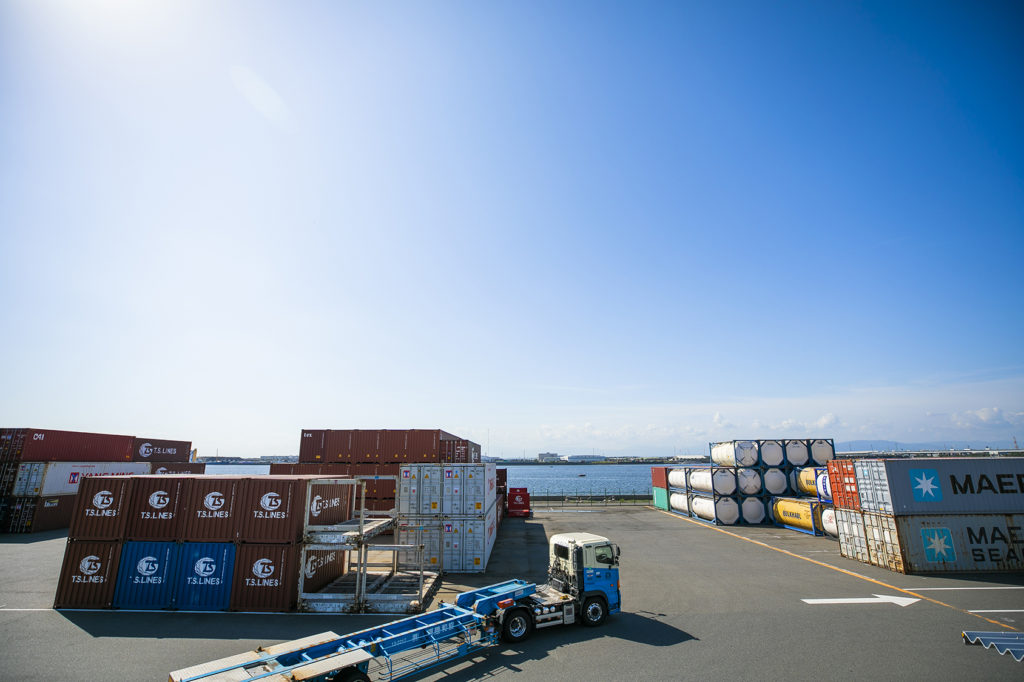
We proposed Nishihama Van Pool where storage anytime and for any period is possible.
The terminal accepts export containers only 10 days before the arrival of the ship. But at Nishihama Van Pool, containers can be stored anytime and for any period. Using this advantage, we proposed storing containers at Nishihama Van Pool until the terminal opens and then transferring them there from Nishihama Van Pool.
Further, we proposed short drayage between Nishihama Van Pool and the terminal. Due to concerns over changes to terminal opening due to ship delays, we explained they had nothing to worry about after delivery to Nishihama Van Pool as we confirm the date of port arrival and carry out drayage at Nishihama.
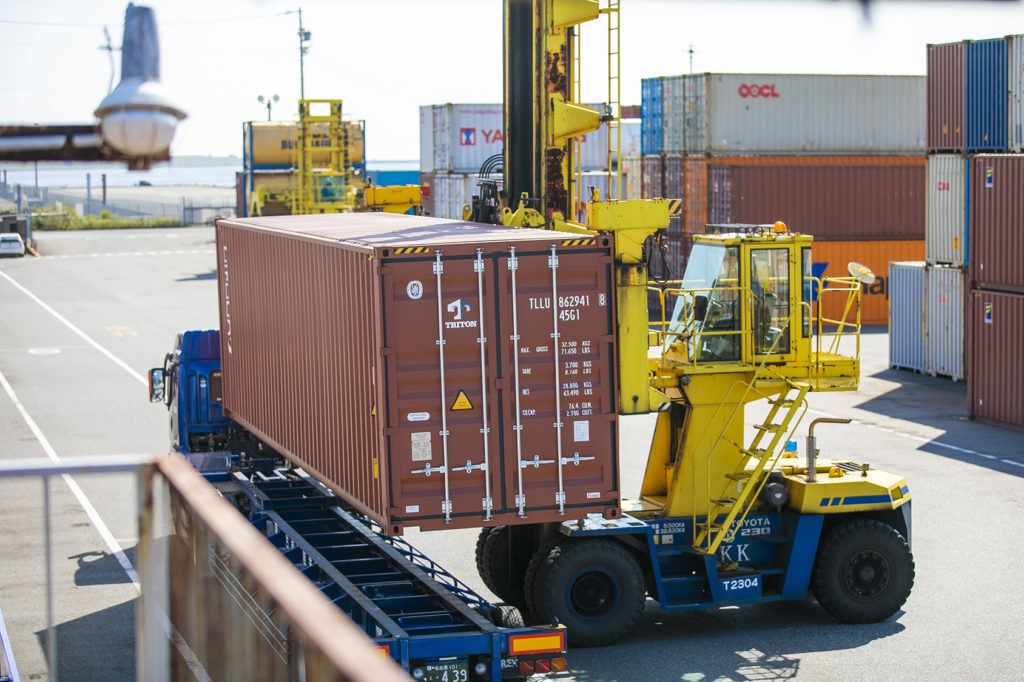
We were able to minimize the impact on their production system and schedule adjustments.
The storage of containers at Nishihama Van Pool itself increases the shipper’s costs. But vanning in advance makes it possible to alleviate the tight situation in the shipper’s warehouse. As a result we were able to minimize the impact on their production system and schedule adjustments.
We were also able to avoid intensive work by doing work in advance to spread the load. The shipper has no concerns about processing after delivery to Nishihama Van Pool by requesting drayage. Realistically, the shipper alone did not have the mobility to perform drayage, and was satisfied it could meet its deadlines.
and other matters, click here